By: Manpreet Kaur
In today’s dynamic business environment, supply chain agility has become a critical factor for organizations striving to stay competitive and resilient. As businesses expand globally, their supply chains become more complex, involving multiple tiers of suppliers. To enhance flexibility, responsiveness, and overall efficiency, it is imperative for companies to foster collaboration across all levels of their supply chain. This article explores the significance of multi-tier supplier collaboration and its pivotal role in achieving supply chain agility.
Multi-tier supplier collaboration refers to the close and strategic partnership between a focal company and its suppliers, as well as the suppliers of those suppliers (and so forth). Traditionally, companies have primarily focused on establishing strong relationships with their immediate suppliers, overlooking the potential risks and opportunities that lie deeper within the supply chain.
The Importance of Multi-Tier Collaboration:
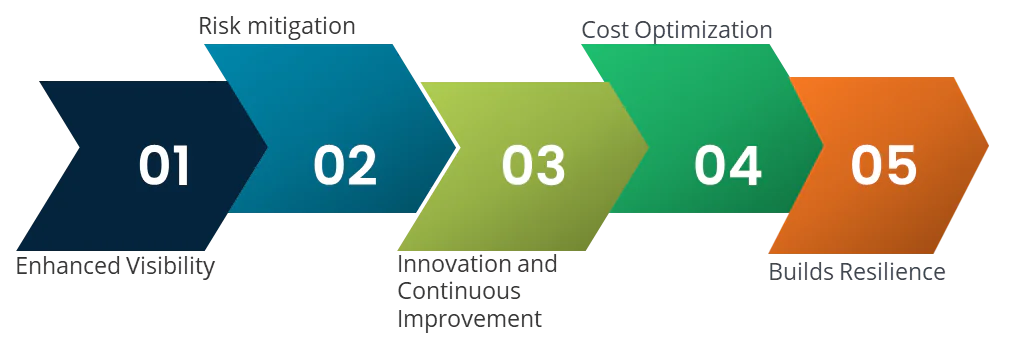
Enhanced Visibility:
One of the primary benefits of multi-tier supplier collaboration is improved visibility across the entire supply chain. When companies collaborate with their direct suppliers as well as those at lower tiers, they gain insight into the entire production process. This enhanced visibility enables better forecasting, inventory management, and risk mitigation. Companies can proactively identify potential disruptions or bottlenecks and implement strategies to address them before they impact the supply chain.
Risk Mitigation:
Supply chains are susceptible to various risks, ranging from natural disasters and geopolitical events to economic downturns and supplier bankruptcies. Multi-tier collaboration helps in diversifying risks by providing alternative sources and creating redundancies in the supply network. If a disruption occurs at one tier, companies can quickly pivot to alternate suppliers or implement contingency plans, minimizing the impact on the overall supply chain.
Innovation and Continuous Improvement:
Collaboration fosters an environment of innovation and continuous improvement. When companies engage with suppliers at multiple tiers, they can tap into the diverse expertise and capabilities of each partner. This collaborative approach encourages the exchange of ideas, best practices, and technological advancements. It enables the integration of new technologies, processes, and materials, keeping the supply chain agile and competitive in a rapidly evolving market.
Cost Optimization:
Collaboration allows for more efficient resource allocation, reducing excess inventory and minimizing waste. Companies can work together to streamline processes, negotiate better deals, and optimize logistics, ultimately leading to cost savings.
Builds Resilience:
Supply chain resilience relies on the ability to adapt to unforeseen circumstances. Multi-tier collaboration strengthens the entire supply chain, making it more resilient to external shocks, market fluctuations, and other uncertainties.
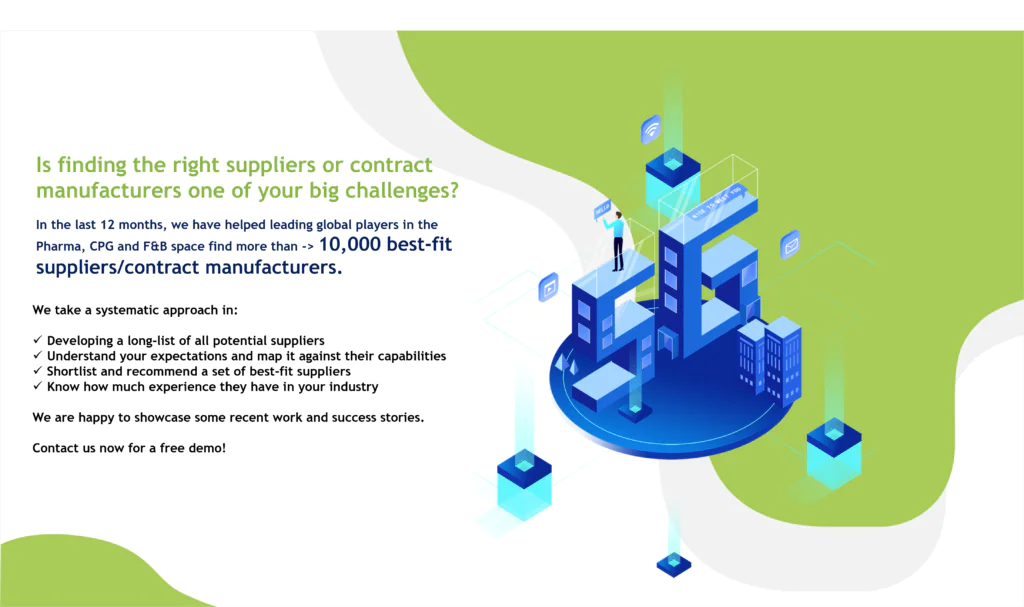
Contact us now to solve your procurement problems!
Author’s Details
Manpreet Kaur
Assistant Manager Presales – Sourcing and Procurement Intelligence
Manpreet is a presales specialist at Infiniti Research and has expertise in sales, business strategy execution, and innovative solution design. She is actively involved in supporting clients from F&B, CPG, Healthcare, Pharma, Chemicals, BFSI, Oil & Gas and Automotive sectors.