By: Manpreet Kaur
In today’s globalized economy, optimizing supply chain networks has become a vital priority for businesses across various industries. Supply chain network optimization is the process of strategically designing, analyzing, and improving the flow of goods, information, and finances from suppliers to end customers. By implementing effective optimization techniques, you can gain a competitive edge, enhance operational efficiency, and maximize profitability.
Supply chain executives and supply chain people model these highly complex networks, navigating supply chain challenges such as breaks in supply and network stress. They work towards consolidated optimal footprint and incremental network changes within unconstrained capacity networks, all while considering the supply chain organizational structure and modeled Supply Chain scope.
Optimization-derived supply chain network designs are crafted through multi-objective network optimization, utilizing mathematical optimization and algorithmic optimization techniques. These methods range from stochastic optimization to combinatorial optimization with Physics-Inspired Graph Neural Networks, addressing both traditional supply chain problems and the evolving dynamics of modern supply chains.
In essence, supply chain functions are intricately woven into the fabric of business operations, and through supply chain network optimization, organizations can streamline processes, mitigate risks, and ultimately thrive in today’s competitive marketplace.
For more details on SpendEdge services
Business constraints in network optimization
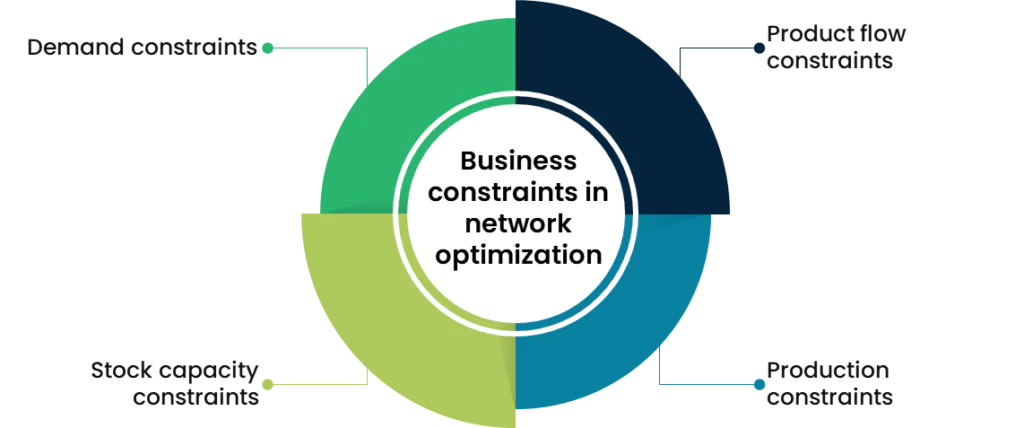
Demand constraints:
Demand constraints refer to limitations on the quantity of goods or services that customers require within a given timeframe. These constraints influence decisions on inventory levels, production schedules, and distribution strategies to ensure customer satisfaction while minimizing costs.
Product flow constraints:
Product flow constraints restrict the movement of goods through the supply chain network, often due to capacity limitations, transportation restrictions, or regulatory requirements. Overcoming these constraints involves optimizing routing, warehouse operations, and inventory management to maintain efficient product flow.
Stock capacity constraints:
Stock capacity constraints pertain to the maximum quantity of inventory that can be stored at various points in the supply chain. Balancing inventory levels with available storage space is crucial for avoiding stockouts, excess holding costs, and disruptions to operations.
Production constraints:
Production constraints encompass limitations on manufacturing capabilities, such as equipment capacity, labor availability, or raw material shortages. Managing production constraints involves optimizing production schedules, resource allocation, and sourcing strategies to meet demand while maximizing efficiency and minimizing costs.
3 phases that occur within a successful supply chain optimization process
A successful supply chain optimization process typically unfolds in three key phases:
Supply Chain Design:
This phase involves delineating network design strategies, including the strategic placement of warehouse facilities and the optimization of product flows among them. It encompasses setting strategic objectives such as demand forecasting, establishing supply sources, and orchestrating manufacturing operations through meticulous planning and scheduling.
Supply Chain Planning:
Here, the focus shifts towards crafting a comprehensive strategic blueprint for supply chain deployment. Activities include inventory planning and the harmonization of assets to optimize the seamless delivery of goods, services, and information from suppliers to customers. The overarching goal is to strike a delicate balance between supply and demand dynamics.
Supply Chain Execution:
The final phase centres on the implementation of execution-oriented applications and systems. This encompasses a spectrum of activities, including warehouse and inventory management, transportation management, and global trade management. Additionally, it involves deploying real-time decision support tools, enhancing supply chain visibility, and managing order fulfillment processes efficiently
Why is supply chain optimization important?
Supply chain optimization is crucial for businesses across industries due to several compelling reasons. Firstly, it enhances operational efficiency by streamlining processes and reducing unnecessary costs. By optimizing the flow of goods, information, and finances from suppliers to end customers, companies can minimize redundancies, eliminate bottlenecks, and improve resource utilization. This efficiency translates into cost savings, which directly contribute to increased profitability and competitiveness in the market.
Secondly, supply chain optimization enables companies to meet customer demands more effectively. By aligning supply with demand through accurate forecasting and inventory management, businesses can ensure timely delivery of products and services. This leads to higher customer satisfaction levels, strengthens brand loyalty, and fosters long-term relationships with clients. In today’s dynamic market environment, where customer expectations are constantly evolving, the ability to adapt and respond promptly is paramount for sustained success.
Thirdly, supply chain optimization helps mitigate risks and uncertainties inherent in global supply chains. By identifying vulnerabilities and implementing robust risk management strategies, companies can proactively address potential disruptions such as natural disasters, geopolitical conflicts, or supply chain disruptions. This resilience not only safeguards business continuity but also enhances stakeholders’ confidence, including investors, partners, and customers, thereby bolstering the company’s reputation and credibility.
Moreover, supply chain optimization facilitates innovation and agility within organizations. By fostering collaboration among different stakeholders and leveraging advanced technologies such as data analytics, artificial intelligence, and automation, companies can drive continuous improvement and innovation across the supply chain. This agility enables businesses to adapt quickly to changing market dynamics, seize emerging opportunities, and stay ahead of competitors, positioning them for sustained growth and success in the long term.
Lastly, supply chain optimization contributes to sustainable and responsible business practices. By optimizing transportation routes, reducing waste, and minimizing carbon emissions, companies can contribute to environmental conservation and social responsibility initiatives. This not only aligns with ethical business practices but also resonates with environmentally conscious consumers and regulatory requirements, enhancing the company’s reputation and attractiveness as a socially responsible entity. In summary, supply chain optimization is essential for driving efficiency, resilience, innovation, and sustainability, ultimately enabling businesses to thrive in today’s competitive landscape.
Request a free trial of our services at SpendEdge that can help you with procurement
Key features of effective supply chain optimization
Visibility:
Visibility refers to the ability to track and monitor the movement of goods, information, and finances across the entire supply chain in real-time. It involves having a clear, comprehensive view of inventory levels, order statuses, transportation routes, and other critical data points. With enhanced visibility, businesses can identify inefficiencies, anticipate potential disruptions, and make informed decisions to optimize processes and improve overall performance.
Order Management:
Order management involves the efficient processing and fulfillment of customer orders from initiation to delivery. This includes order capture, order processing, inventory allocation, and shipment tracking. Effective order management systems ensure accuracy, timeliness, and reliability in order fulfillment, leading to enhanced customer satisfaction and loyalty. By streamlining order management processes, businesses can reduce order processing times, minimize errors, and meet customer demands more effectively.
Intelligence:
Intelligence refers to the use of advanced technologies such as artificial intelligence (AI), machine learning, and predictive analytics to gather, analyze, and interpret data for decision-making purposes. Intelligent supply chain systems can anticipate demand patterns, identify optimization opportunities, and proactively respond to changing market conditions. By leveraging intelligence, businesses can gain valuable insights into their supply chain operations, optimize resource allocation, and drive continuous improvement and innovation.
Inventory Tracking:
Inventory tracking involves monitoring the movement and storage of inventory throughout the supply chain, from raw materials to finished goods. It includes tracking stock levels, inventory locations, and inventory turnover rates in real-time. Effective inventory tracking systems enable businesses to optimize inventory levels, reduce carrying costs, and prevent stockouts or excess inventory situations. By maintaining accurate inventory records and implementing inventory optimization strategies, businesses can improve inventory management efficiency and maximize profitability.
Reporting and Analytics:
Reporting and analytics involve the generation of meaningful insights and performance metrics based on supply chain data. It includes the analysis of key performance indicators (KPIs), trend analysis, and performance benchmarking to evaluate supply chain performance and identify areas for improvement. By leveraging reporting and analytics tools, businesses can monitor performance against goals, track performance trends over time, and make data-driven decisions to optimize supply chain operations. Additionally, reporting and analytics facilitate communication and collaboration among supply chain stakeholders, enabling informed decision-making and continuous improvement efforts.
Conclusion
In conclusion, the significance of supply chain optimization cannot be overstated in today’s dynamic business landscape. By effectively optimizing supply chain networks and addressing challenges such as demand constraints, product flow constraints, stock capacity constraints, and production constraints, businesses can achieve optimal efficiency and maximize profitability. The three phases of supply chain optimization – design, planning, and execution – provide a structured approach to enhancing operations and meeting customer demands effectively
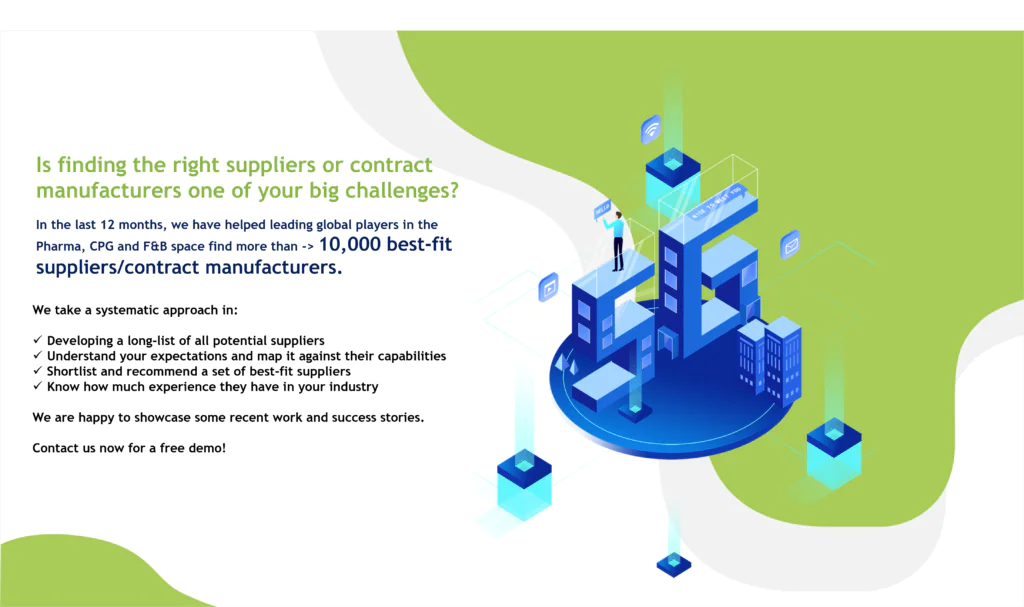
Get in touch with our professionals and see how it helps your business
Author’s Details
Manpreet Kaur
Assistant Manager Presales – Sourcing and Procurement Intelligence
Manpreet is a presales specialist at Infiniti Research and has expertise in sales, business strategy execution, and innovative solution design. She is actively involved in supporting clients from F&B, CPG, Healthcare, Pharma, Chemicals, BFSI, Oil & Gas and Automotive sectors.