The construction industry, integral to global infrastructure development, encounters inherent complexities that profoundly affect both operational efficiency and long-term viability. Central to these complexities is the management of construction supply chains, a pivotal element that directly influences project timelines, budget adherence, and the overall success of construction projects. This article delves into the multifaceted nature of supply chain risks in the construction sector, offering strategic insights to manage these risks effectively.
Supply Chain Management (SCM) in construction is not merely about circumventing negative outcomes; it’s about capitalizing on opportunities to enhance efficiency and drive sustainability forward. The industry faces a myriad of challenges, from volatile material costs and supply chain disruptions to stringent regulatory demands and labor shortages. Each of these elements has the potential to significantly disrupt project timelines and inflate costs, thereby impacting overall project delivery.
This comprehensive exploration will address the various challenges that impede smooth supply chain operations, ranging from supply chain risks to issues with material management and regulatory compliance. Additionally, the article outlines both traditional and innovative strategies for effective risk management. By incorporating case studies, highlighting technological advancements, and discussing proactive mitigation tactics, we aim to equip industry professionals with the necessary tools to navigate the complexities of construction supply chains. This guidance is designed to ensure not only the success of individual projects but also the sustainability and growth of the construction industry at large.
Main Challenges in Construction Supply Chains
Effective Supply Chain Management (SCM) in construction is pivotal, yet fraught with challenges that can derail projects if not adeptly managed. Below we delve into the key issues that often impede the smooth functioning of construction supply chains, exploring each challenge in greater detail to provide a comprehensive understanding:
- Supply Chain Risk: The supply chain serves as the backbone of project delivery in construction. Any disruptions within this chain can lead to significant project delays and substantial budget overruns. These disruptions may stem from a variety of sources, including logistical failures, strikes, political instability, and natural disasters. The ripple effects of such disturbances can halt production, inflate costs due to urgent sourcing needs, and extend project timelines significantly.
- Materials Management: The availability and quality of materials are critical factors that directly influence the construction timeline and the structural integrity of the completed projects. Shortages of key materials can cause delays, while subpar material quality can lead to safety concerns and long-term durability issues, necessitating costly repairs and replacements. Moreover, fluctuations in material costs can impact the overall budget, making cost management more challenging.
- Architect and Third-party Supplier Relations: Effective coordination and communication between architects, engineers, and third-party suppliers are vital for the seamless delivery of materials and services according to project specifications. Miscommunication can lead to non-compliance with architectural designs, resulting in rework and delays. Establishing a clear communication channel, regular updates, and feedback loops is essential to synchronize expectations and project realities, ensuring all parties are aligned with the project goals.
- Construction Schedule and Materials: Adhering to a precise construction schedule is essential for the effective management of labor and resource allocation. Delays in the arrival of critical materials can disrupt the schedule, leading to inefficient labor use and increased costs. Effective schedule management involves detailed planning and the ability to quickly adapt to changes. This requires robust project management tools and techniques to forecast potential delays and dynamically adjust work plans accordingly.
- Regulatory Compliance and Permits: Navigating the complex landscape of local and international regulations, as well as securing the necessary permits, is a crucial challenge in construction SCM. Delays in obtaining permits or failing to comply with regulations can stall projects indefinitely. It is crucial for supply chain managers to have a thorough understanding of all applicable regulations and to maintain strong relationships with regulatory bodies.
- Technology Integration: Integrating technology into SCM processes can greatly enhance efficiency but poses its own challenges. The selection of appropriate technology solutions that are compatible with existing systems, training staff to use new tools effectively, and ensuring cybersecurity measures are in place are key hurdles that need to be addressed to harness the full potential of technological advancements.
By understanding and addressing these critical challenges, construction firms can enhance their supply chain management capabilities, leading to smoother project execution and better outcomes. Each of these areas requires focused strategies and an integrated approach to risk management to mitigate impacts and drive project success.
Strategies for Risk Management
Effective risk management within construction supply chain management (SCM) is essential to ensure project success and sustainability. It requires a proactive approach to anticipate, address, and mitigate potential issues before they escalate. Below, we expand on comprehensive strategies that can be implemented to enhance risk management in construction SCM:
- Transparent Supply Chain:
- Real-time Data Sharing: Implement tools and systems that provide real-time visibility into the supply chain. This can include the use of IoT devices and cloud-based platforms that track material shipments, inventory levels, and project progress, ensuring that all stakeholders have up-to-date information.
- Standardized Reporting: Develop standardized reporting protocols and dashboards that allow for quick assessments of supply chain health. This can help identify bottlenecks or delays early, allowing for timely interventions.
- Strengthening Supplier Relationships for Effective Supply Chain Risk Management:
- Supplier Integration: Involve key suppliers early in the project planning phase to leverage their expertise and ensure materials and components are delivered in alignment with project timelines and specifications.
- Long-term Partnerships: Move beyond transactional relationships by developing long-term partnerships with suppliers. This could include joint ventures or shared risk and reward contracts that incentivize supplier performance and investment in quality improvements.
- Regular Evaluations and Feedback: Establish a routine of regular supplier evaluations followed by constructive feedback sessions. This helps maintain high standards and continuous improvement in the supply chain.
- Risk Assessment and Contingency Planning:
- Comprehensive Risk Audits: Conduct comprehensive risk audits that consider everything from geopolitical factors affecting supply chains to local labor market conditions. Use this information to inform the risk management strategy.
- Scenario Planning: Engage in scenario planning exercises that address potential disruptions, from natural disasters to sudden market fluctuations. Develop action plans that can be quickly deployed in response to these scenarios.
- Flexible Contingency Funds: Set aside contingency funds that can be accessed in the event of critical supply chain disruptions. These funds can cover the cost of expediting shipments, switching suppliers, or other emergency responses.
- Diversification of Supply Chain:
- Multi-sourcing Strategies: Avoid dependency on single suppliers by establishing relationships with multiple suppliers for critical materials. This reduces the risk of major disruptions if one supplier faces a setback.
- Global Sourcing: Expand sourcing strategies to include global suppliers, which can not only reduce costs but also buffer local supply issues.
- Advanced Technological Tools:
- Predictive Analytics: Use predictive analytics to forecast potential supply chain disruptions. Machine learning models can analyze historical data and predictive indicators to alert managers about risks that may affect the supply chain.
- Blockchain for Transparency: Implement blockchain technology to enhance transparency and accountability in the supply chain. Blockchain can securely track the provenance and status of materials as they move through the supply chain, reducing the risk of fraud and ensuring compliance.
- Enhanced Communication Strategies:
- Communication Protocols: Establish clear communication protocols that dictate how and when to communicate risks. This ensures that all relevant stakeholders are promptly informed about potential issues that could impact the project.
- Stakeholder Engagement: Regularly engage with all stakeholders, including suppliers, contractors, and clients, to discuss potential risks and collaboratively develop mitigation strategies.
Technological Innovations in Risk Management
In the dynamic field of construction, the adoption of cutting-edge technologies plays a crucial role in enhancing risk management strategies. This section explores three pivotal technological innovations—Digital Twin Technology, AI and Machine Learning, and Drones and Automated Vehicles—that are transforming how risks are identified, analyzed, and mitigated in construction supply chains.
Digital Twin Technology
Digital Twin Technology involves creating a digital replica of a physical construction site or infrastructure project. This virtual model is continuously updated with real-time data collected from various sensors on-site, allowing project managers and teams to simulate different scenarios and predict potential problems before they occur. Here’s how it benefits risk management:
- Predictive Maintenance: By monitoring the condition of equipment and structures, digital twins can predict when maintenance should be performed, preventing unexpected failures that could cause costly delays.
- Scenario Testing: Digital twins allow for the testing of various construction approaches in a virtual environment, enabling the identification and mitigation of risks associated with structural designs, materials, and construction processes.
- Integration and Oversight: They provide a holistic view of the project, integrating data across different stages of construction. This comprehensive oversight helps in detecting discrepancies early, ensuring compliance with design specifications and regulatory standards.
AI and Machine Learning
AI and Machine Learning are revolutionizing risk management in construction by processing vast amounts of data to identify patterns, predict outcomes, and automate complex decision-making processes. Key applications include:
- Risk Prediction: AI algorithms analyze historical data and ongoing project data to forecast potential risks, from material shortages to workforce disruptions.
- Resource Optimization: Machine learning models optimize the allocation of resources, including labor and materials, by predicting project flow changes and adjusting allocations proactively to minimize waste and inefficiency.
- Quality Control: AI-driven tools perform real-time analysis of construction quality, identifying deviations from planned specifications or potential structural issues that could lead to future risks.
Drones and Automated Vehicles
Drones and automated vehicles are increasingly used on construction sites for a variety of tasks that contribute to risk management:
- Site Surveying and Inspection: Drones provide aerial views and detailed images of construction sites, making it easier to inspect hard-to-reach areas and monitor ongoing work without the need for physical presence, which reduces safety risks for workers.
- Material Transport: Automated vehicles are used to transport materials across large construction sites efficiently, reducing the likelihood of delays and human error, while also improving safety by reducing on-site traffic.
- Data Collection: Both drones and automated vehicles are equipped with sensors and cameras that collect data essential for updating digital twins and feeding AI models, enhancing the overall accuracy of risk assessments and decision-making processes.
These technological innovations are integral to modern construction projects, offering new ways to manage risks more effectively, enhance operational efficiencies, and ensure the successful completion of projects. By integrating these technologies into their risk management frameworks, construction companies can not only mitigate current risks but also anticipate future challenges, positioning themselves at the forefront of industry advancements.
Environmental and Sustainability Considerations
In the construction industry, environmental and sustainability considerations are becoming increasingly crucial, not only for compliance with evolving regulatory requirements but also for driving corporate responsibility and enhancing public perception. This section focuses on two key aspects: Green Procurement and Risk Mitigation through Sustainability, which are pivotal for embedding environmental stewardship into construction supply chain management.
Green Procurement
Green Procurement involves the purchasing of materials and services that have minimal adverse environmental impacts. It is a proactive approach aimed at promoting eco-friendly practices throughout the supply chain. Here’s how it integrates into construction:
- Selection of Sustainable Materials: Prioritizing the use of renewable, recyclable, and less toxic materials that contribute to sustainability, such as certified wood, recycled metal, or low-VOC (Volatile Organic Compounds) paints.
- Supplier Sustainability Assessments: Evaluating suppliers based on their environmental performance and commitment to sustainable practices. This can include their use of energy-efficient processes, proper waste management techniques, and adherence to environmental management standards like ISO 14001.
- Lifecycle Analysis: Implementing lifecycle analysis to assess the environmental impact of materials over their entire lifecycle, from extraction and manufacturing to disposal. This helps in selecting materials that not only serve the project’s needs but also minimize long-term environmental damage.
Risk Mitigation through Sustainability
Sustainability in construction goes beyond environmental benefits, playing a crucial role in risk mitigation. Sustainable practices can significantly reduce risks associated with environmental regulation compliance, resource scarcity, and community relations. Here’s how sustainability contributes to risk mitigation:
- Regulatory Compliance: By adopting sustainable practices, construction projects are better equipped to comply with environmental regulations, which are becoming stricter globally. This reduces the risk of fines, project delays, and reputational damage associated with non-compliance.
- Resilience to Resource Scarcity: Sustainable practices often involve efficient resource use and waste reduction, which shield projects from the volatility of resource availability and prices. For example, using water-recycling systems on construction sites not only conserves water but also ensures that projects are less vulnerable to disruptions in water supply.
- Enhanced Community and Stakeholder Engagement: Sustainable projects tend to receive more support from local communities and stakeholders, including investors increasingly focused on environmental, social, and governance (ESG) criteria. This support can facilitate smoother project execution and open up access to new funding opportunities.
Incorporating green procurement and sustainability-focused risk mitigation strategies into construction supply chain management helps companies achieve more resilient and responsible operations. These practices not only address immediate environmental impacts but also contribute to the long-term viability and success of construction projects, creating a positive feedback loop that benefits both the industry and the communities it serves.
Further Reading
- For more information on the different types of construction industry sectors and their specific challenges, click here.
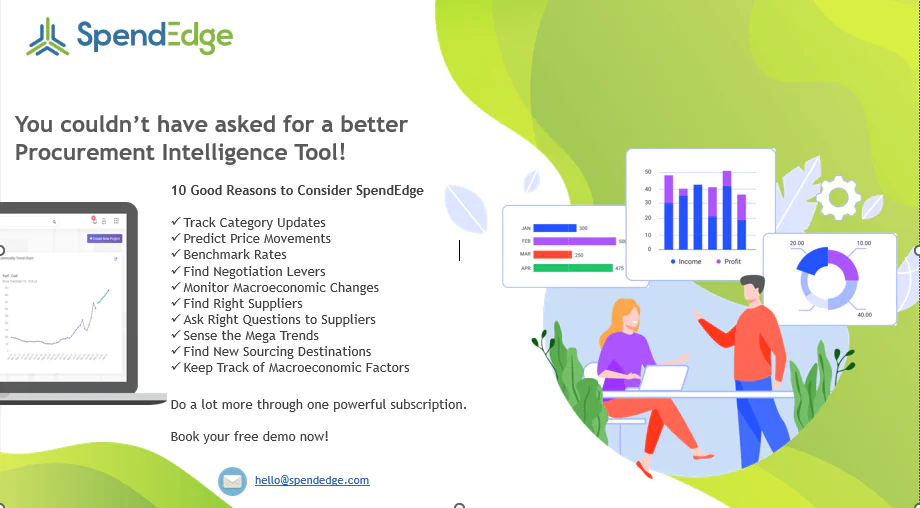