The personal care industry is highly competitive, with brands persistently striving for consumer attention and loyalty. In such a landscape, every aspect of production, including labeling, can significantly impact a company’s bottom line. Cost model analysis is an essential tool that can help businesses in this sector save money, improve efficiency, and enhance their competitive edge. Here’s how:
Understand the Concept
Cost model analysis is a systematic approach to understanding and optimizing the costs associated with products. This process involves evaluating all the variables that contribute to the final cost of a finished product, including materials, printing processes, labor, equipment, logistics and supplier margins and variable costs. By breaking down these elements, companies can identify areas for cost reduction and efficiency improvements, ensuring cost accuracy.
Key Cost Components Impacting Label Costs
- Material Costs: The type of material used for labels such as paper, plastic, or eco-friendly options can significantly impact costs. Cost modeling helps in comparing the prices and benefits of different materials, enabling businesses to select the most cost-effective option without compromising on quality.
- Printing Techniques: Different printing techniques, such as digital printing, flexography, and offset printing, have varying cost structures. Cost modeling can analyze the suitability and cost-efficiency of these techniques based on the volume and design complexity of the labels required.
- Labor and Overhead: Labor costs and overheads, including equipment maintenance and utility expenses, contribute to the overall labeling costs. Through cost modeling, companies can streamline their processes to reduce these expenses.
- Logistics and Distribution: The costs involved in shipping labels to manufacturing sites or distribution centers can be optimized through strategic planning. Through cost modeling it is possible to understand the total costs involved and identify the most efficient and cost-effective logistics solutions.
Strategic Benefits of Conducting Cost Model Analysis
Cost Reduction:
By identifying and addressing inefficiencies in the overall process, companies can significantly reduce their overall costs. This reduction can be achieved through selecting more affordable materials, optimizing printing processes, and improving labor productivity.
Enhanced Budget Management:
Cost modeling provides a detailed breakdown of all expenses associated with labeling. This transparency helps in better budget planning and allocation, ensuring that resources are used effectively.
Improved Supplier Negotiations:
With a clear understanding of the cost components, companies can negotiate better terms with suppliers. This knowledge empowers businesses to secure lower prices for materials and services, further driving down costs.
Sustainability and Compliance:
The personal care industry is increasingly focused on sustainability. Cost modeling can assist in evaluating the cost implications of using eco-friendly materials and processes, helping companies make informed decisions that align with their sustainability goals and regulatory requirements.
Competitive Advantage:
By optimizing labeling costs, companies can reallocate savings to other areas such as marketing, product development, or price reductions, enhancing their competitiveness in the market. This strategic reallocation can positively impact both spend and revenue, driving overall business success.
How SpendEdge Can Help?
Our Cost Modeling techniques have helped our global clients achieve high level cost efficiency and drive profitability. We have conducted cost modeling studies across industries for different products and services for our clients. We have the capabilities of developing deep dive cost models providing clear breakdown of the key cost components and visibility on the major cost drivers. Some of the components that we can cover in our cost models are as outlined below.
Raw Materials and Inputs, Labor, Wages of the production staff, Process, Transportation, Equipment, Manufacturing Supplies, Power Consumption etc.
Selling and Administration, Facility Rental, Utilities, Shipping and Handling, Indirect Supplies, Legal Fees, Equipment Depreciation, Insurance etc.
Capital Cost, Depreciation Cost, Maintenance Cost, Overhaul Cost, Repair Cost, Product Life Cycle, Material Content, Order Processing Costs.
ricing of different variants of products, CAPEX details, Movement of key cost drivers, Negotiation levers, Impact levels of each cost component, Qualitative insights based on research findings, Visibility on detailed calculations and sources and much more.
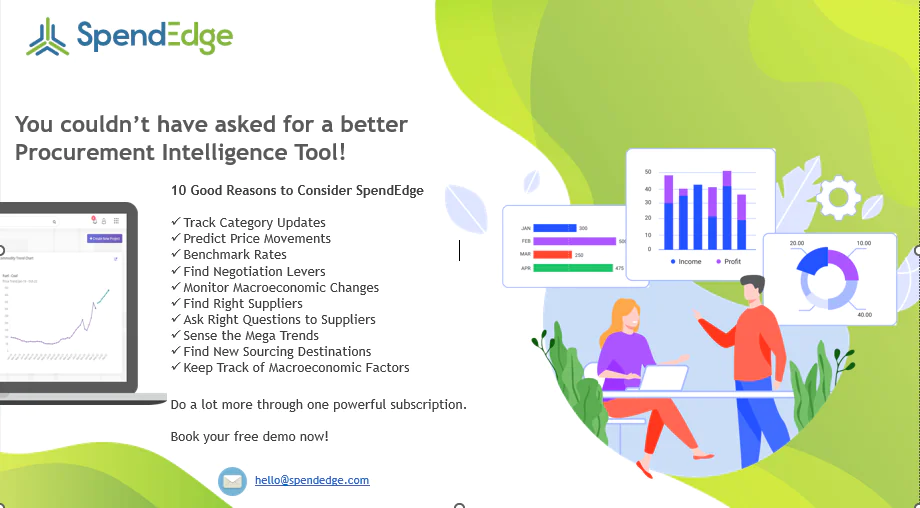
If you’re looking to enhance your cost management strategies and improve your bottom line, contact us today for a tailored proposal on how our cost modeling services can benefit your business.