The global biotechnology market, valued at $1,300 billion, is experiencing growth driven by customized treatments and an aging population. However, challenges such as competition from generics, government-regulated pricing, and evolving regulations under the Affordable Care Act can hinder profit potential. A key barrier to sustained growth in pharma and biotech sectors is the suboptimal execution of manufacturing strategies. The industry’s historic performance on quality is commendable, but evolving expectations for quality at the molecular level require a leap forward.
Enter Pharma 4.0 smart manufacturing, a transformative technology that guarantees quality by design through sensors, AI, big data, and cloud computing. This shift not only enhances real-time asset health monitoring and predictive maintenance but also helps manufacturers contain operational risks. Despite its promise, many pharma companies are taking a cautious approach, prioritizing the security and readiness of interconnected factory environments. To embrace Pharma 4.0 smart manufacturing successfully, pharma and biotech manufacturers need clear, data-driven supply market intelligence and the right technology partners.
What is Pharma 4.0 Smart Manufacturing?
Pharma 4.0 Smart Manufacturing refers to the integration of advanced technologies like IoT, AI, robotics, and digital twins into pharmaceutical production processes. This innovative approach enables real-time data collection, automation, and enhanced decision-making, driving operational efficiency, improved quality control, and faster time-to-market for pharmaceutical products. By embracing Pharma 4.0, companies can achieve a more flexible, scalable, and sustainable manufacturing environment.
How Pharma 4.0 Smart Manufacturing Eliminates Costly Shopfloor Rigmaroles
Pharma 4.0 smart manufacturing benefits
- Right decisions through big-data-based analytics
- A performance-aware framework for factory ops
- Sustainable manufacturing at scale with close-to-nil human errors
- Full automated flexible production with improved cybersecurity infra
Right decisions through big-data-based analytics
Given the manifold challenges in their way, participants in the pharma and biotech sectors must do more with less resources while making significant financial gains. Smart manufacturing, a concept that emerged in the early 2000s, is seeing more uptake across sectors, thanks to its proven capability to deliver high-quality customized outputs, minimize costs, and conserve scarce resources. Essentially, smart manufacturing methods leverage current and historical data from the production activity to draw deep and accurate insights to deliver that big-picture view CXOs need to make better decisions around processing, labor, and machinery.
A performance-aware framework for factory ops
Smart manufacturing facilities, backed by an army of sensors (“things”), as well as cloud-based storage of files and data, are turbocharging data sharing within the pharma enterprise like never before to optimize performance on multiple fronts: energy consumption, waste control, downtime minimization, and emission cutbacks.
Sustainable manufacturing at scale with close-to-nil human errors
With smart sensors continuously keeping a watch on people and ML/AI technologies automating and smoothing workflows, human lapses arising out of inexperience, inattention, and fatigue, as well as catastrophic machine failures have appreciably diminished. The increasing share of renewable energy by smart and forward-looking biotech enterprises is helping them make remarkable progress toward climate goals and meet ever-rising environmental mandates. Based on real-time insights, smart manufacturers in pharma are tailoring new products such as nanotechnology-based drug delivery systems, besides shrinking the drug discovery-to-clinical-trial cycle.
Full automated flexible production with improved cybersecurity infra
More importantly, smart manufacturing is enabling drug makers to continuously recalibrate production schedules in line with demand troughs and crests in the market. Of course, any paradigmatic shift in the industrial space comes with a baggage of concerns, no matter how small it might be. The tiny fraction of manufacturers who still have hesitations about smart factory adoption simply because of undue concerns about cybercrimes risk missing the boat and the associated benefits altogether! By budgeting for cybersecurity and strengthening their organization’s cyber posture, smart manufacturers can enjoy the fruits of digitally enabled production while keeping cyber risks in check.
Ready to transform your pharmaceutical manufacturing with Pharma 4.0 smart technology? To discover how data-driven solutions can boost efficiency, quality, and growth…
Benefits of Generative AI in Procurement
How SpendEdge Drives Success with Pharma 4.0 Smart Manufacturing Solutions
-
Leverage advanced analytics to optimize production workflows and instantly detect deviations, enhancing operational efficiency and product quality.
-
Use predictive analytics and IoT-enabled sensors to proactively identify and address potential risks, ensuring smooth, uninterrupted manufacturing processes.
-
Align manufacturing strategies with customer demands by selecting the right technology partners for seamless, future-ready digital transformation.
-
Conduct in-depth supplier evaluations to secure long-term, mutually beneficial partnerships that drive innovation and ensure consistent, high-quality production.
Boost Real-Time Factory Floor Visibility
At SpendEdge, we provide pharma clients with comprehensive 360-degree views of their shopfloor activities. By leveraging advanced analytics, we help identify bottlenecks that impede productivity and negatively affect the customer experience. With Pharma 4.0 smart manufacturing solutions, real-time visibility is achieved, ensuring immediate alerts on any deviations from the ideal process. This proactive approach enables timely interventions, minimizing delays, and optimizing workflow, thus enhancing overall efficiency and ensuring higher-quality output.
Assess and Mitigate Production Risks
With over two decades of expertise in sourcing and risk management, SpendEdge assists pharma and biotech companies in identifying and mitigating potential biological, chemical, and physical hazards in their production processes. Our Pharma 4.0 smart manufacturing strategies incorporate predictive analytics and IoT-enabled sensors to foresee risks before they disrupt production. By proactively addressing these risks, we help clients safeguard the quality and consistency of their products, reducing downtime and maintaining smooth operations.
Match Dynamically Evolving Customer Expectations Around Digitization
Pharma manufacturers face ongoing challenges, including lack of shop floor visibility, unplanned machine downtimes, spiraling maintenance costs, and concerns about worker health and safety. These issues can significantly drain budgets and hinder growth. SpendEdge helps manufacturers overcome these obstacles by guiding them in adopting Pharma 4.0 smart manufacturing solutions. Our experts carefully catalog client needs and expectations, ensuring they engage with the right vendors and select the most suitable solutions for seamless digitization. This alignment with customer demands fosters improved operational efficiency and supports future growth.
Find Reliable Suppliers, Forge Sustainable Win-Win Relationships
In the fast-evolving landscape of smart manufacturing, identifying reliable suppliers is crucial. SpendEdge conducts thorough supply-side research to shortlist potential vendors based on a robust assessment framework. We evaluate factors such as price points, lead times, technology capabilities, and past performance. Our expert analysis ensures that pharma manufacturers engage with trustworthy, innovative suppliers who can deliver sustainable solutions. These partnerships not only optimize production but also create long-term value, driving mutual growth and ensuring the success of Pharma 4.0 smart manufacturing adoption.
Discover how Pharma 4.0 can transform your operations. Contact SpendEdge today to explore customized, data-driven strategies that optimize efficiency and ensure quality control.
SpendEdge Helped Pharma Leader Find the Perfect Partner for Seamless Smart Shopfloor Transformation
Client Background:
Our client is a large Europe-based pharmaceutical company specializing in both large and small molecules, with a particular focus on gene therapies, recombinant proteins, stem cell therapies, and targeted medications. To keep pace with evolving market demand, the company aimed to enhance its manufacturing strategy, with an emphasis on biologics. Recognizing the need for operational efficiency, the leadership team identified shopfloor-wide digitization as a key lever to automate processes and boost throughput.
Challenges:
Before moving towards Pharma 4.0, the company needed a clear understanding of the potential benefits of digitization, especially around quality control and operational efficiency. They were particularly interested in exploring the adoption of digital twin technology—virtual, real-time replicas of manufacturing facilities and their equipment. The company was hesitant, needing to assess the level of adoption in the pharmaceutical sector and other industries. Additionally, the leadership team sought a reliable partner to ensure successful, secure implementation with a focus on cyber resilience.
Solutions Offered:
In February 2022, our experienced procurement professionals were brought in to help the client navigate these challenges and identify a technology partner with a proven track record in pharma digitization. Within a short time, our team mapped the digital devices, systems, and processes across the client’s production flow, covering key technologies like IoT, AI, and robotics. By aligning these innovations with the client’s digitization needs, we provided insights into the pros and cons of various smart manufacturing methods used in pharma and other sectors.
Next, our team conducted a comprehensive evaluation of potential vendors capable of implementing the required technologies. This included assessing the costs, benefits, and technical specifications of the proposed solutions. We also prioritized cyber-physical security vendors, carefully matching them to the client’s specific requirements. After a detailed analysis, we presented the client with a shortlist of three vendors, all demonstrating high levels of competence in delivering the needed technologies.
Impact Delivered:
Thanks to our diligent vendor evaluations and deep market knowledge, the client was able to make an informed decision. They engaged a technology consultant to conduct a feasibility study on the digital twin solution and proceeded with the cybersecurity vendor selection process. The client has successfully zeroed in on a vendor from our shortlist, marking a crucial step in their journey towards Pharma 4.0 smart manufacturing.
With our support, the client is now poised to leverage cutting-edge technologies to automate their operations, boost manufacturing efficiency, and ensure enhanced quality control—driving their business forward in a competitive market.
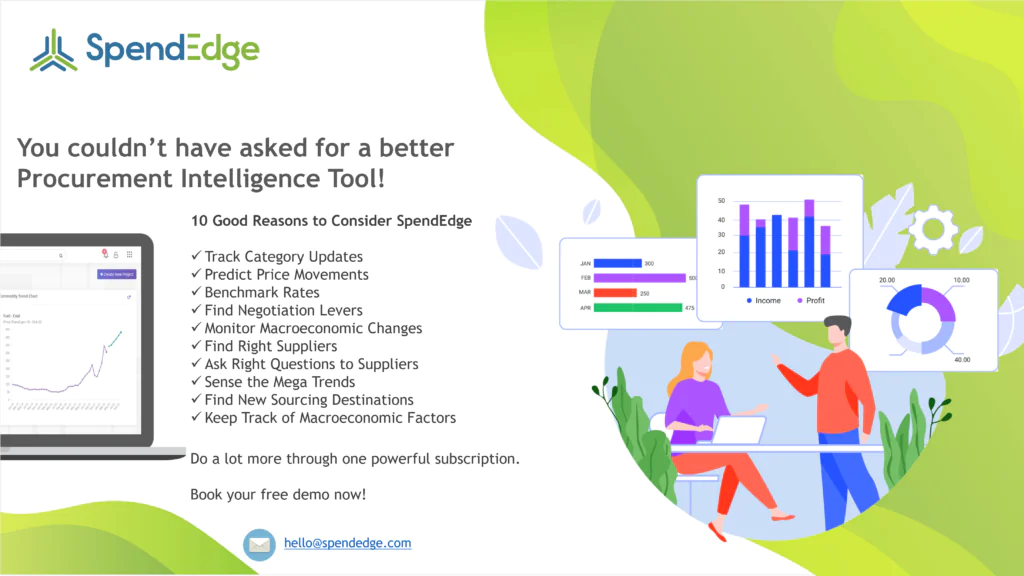
Ready to embrace Pharma 4.0? Connect with SpendEdge to find the right technology partners and drive sustainable growth through smart manufacturing solutions.