The pharmaceutical industry is one of the most complex and heavily regulated sectors globally. With soaring research and development (R&D) costs, stringent compliance requirements, and increasingly intricate supply chain dynamics, reducing costs in the pharma supply chain has become a priority for businesses striving to maintain profitability while ensuring the delivery of life-saving medications.
Challenges
Before diving into cost-reduction strategies, it’s essential to understand the unique challenges that make pharmaceutical supply chain management so intricate:
Regulatory Compliance:
Ensuring adherence to global health and safety standards can be costly and time-consuming.
Cold Chain Requirements:
Many drugs, particularly biologics and vaccines, require temperature-controlled logistics, adding to the expense.
Complex Global Networks:
The pharmaceutical supply chain spans multiple countries and involves numerous stakeholders, increasing complexity.
Demand Volatility:
Unpredictable market demands and global health crises make inventory management and forecasting challenging.
Addressing these challenges requires a blend of innovative strategies, data-driven decision-making, and strategic partnerships.
Proven Strategies for Reducing Costs in the Pharma Supply Chain
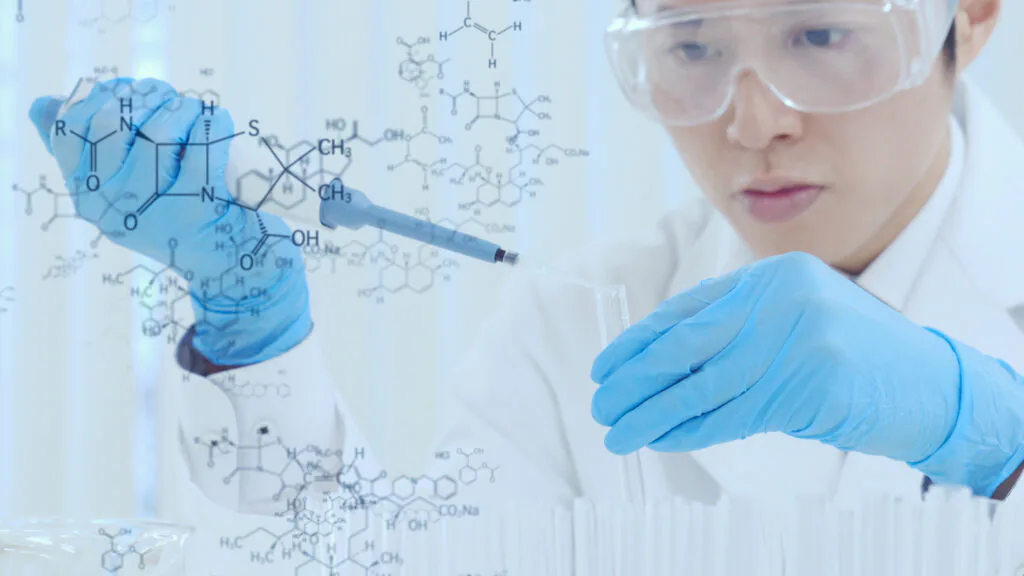
Adopting Advanced Temperature Measurement Techniques
Advanced temperature monitoring solutions, such as data loggers, significantly minimize product spoilage in the pharmaceutical industry by providing continuous real-time temperature tracking. This ensures that temperature-sensitive pharmaceuticals remain within the required temperature range during storage and transportation, effectively preventing spoilage and reducing costs associated with wasted products. Additionally, automated temperature logging systems enhance compliance with regulatory requirements by streamlining the compliance process. By reducing the need for manual checks and minimizing human error, these systems help companies adhere to industry standards, thereby avoiding potential fines and penalties associated with non-compliance.
Furthermore, innovative temperature measurement solutions improve operational efficiency by centralizing data access, making it easier for staff to retrieve information for audits and inspections. This efficiency allows employees to focus on core activities, ultimately lowering operational costs. Automated monitoring systems also reduce manual labor costs by eliminating frequent checks, enabling staff to concentrate on more critical tasks. Continuous monitoring facilitates early detection of equipment failures, preventing costly breakdowns and extending equipment lifespan, which leads to lower maintenance costs overall.
Enhancing Water Production and Distribution Efficiency
Implementing advanced water treatment technologies, such as reverse osmosis and nanofiltration, can significantly reduce water consumption in the pharmaceutical industry. These systems improve the quality of water produced for various applications, allowing companies to optimize their usage. For example, a healthcare products manufacturer successfully reduced its water consumption by 10%, saving over US$3 million over a decade through these optimized systems. Additionally, treating and reusing wastewater minimizes the volume discharged, which often incurs substantial fees. Technologies that enable up to a 98% reduction in wastewater volumes not only lower discharge costs but also align with sustainability goals, contributing to financial stability while optimizing operational costs.
Moreover, optimizing water production can lead to energy savings as well. Implementing systems that adjust heat sanitation based on actual needs rather than continuous operation can result in significant energy reductions, further lowering overall operational costs. Ensuring high-quality water is critical for regulatory compliance; thus, optimized systems help maintain consistent quality and reduce the risk of non-compliance penalties. This proactive approach minimizes potential production downtime due to quality issues. By adopting a comprehensive water management strategy that includes monitoring, recycling, and optimization, pharmaceutical companies can improve resource allocation and operational efficiency, ultimately enhancing productivity and cost-effectiveness across various processes.
Integrating and Evaluating Diagnostic Data While Verifying Instrument Functionality
Routinely confirming the functionality of diagnostic instruments is essential for enhancing instrument reliability in the pharmaceutical industry. This proactive maintenance approach minimizes downtime caused by equipment failures, ensuring that production processes remain efficient and compliant with regulatory standards. By preventing costly interruptions, companies can maintain consistent output and quality, ultimately reducing operational costs associated with delays. Additionally, utilizing advanced diagnostic tools provides real-time data on manufacturing processes, which enhances data accuracy. This accurate information allows for informed decision-making, reducing the likelihood of errors that could lead to product recalls or regulatory fines. Consequently, companies can lower costs associated with quality control and assurance.
Incorporating diagnostic data also streamlines research and development (R&D) processes, enabling better analysis of research outcomes and more effective drug development strategies. By identifying promising candidates earlier in the process, companies can avoid investing in less viable options, thus reducing overall R&D costs. Furthermore, leveraging diagnostic data optimizes clinical trials by enhancing patient selection and trial protocols, which speeds up the process and reduces costs associated with prolonged trials. Continuous assessment of diagnostic data improves inventory management and demand forecasting, leading to reduced wastage and stockouts. This integrated approach not only lowers compliance costs through automated monitoring systems but also enhances manufacturing efficiency by allowing for continuous monitoring of production conditions, ultimately resulting in improved process reliability and reduced costs related to rework or waste.
Ensuring Uniformity in Installed Assets
Standardization of equipment types and models in the pharmaceutical industry significantly improves maintenance efficiency. By creating uniformity, technicians become more familiar with a limited number of asset types, which reduces training time and enhances maintenance effectiveness. This familiarity leads to lower labor costs and minimizes downtime associated with repairs, allowing for more consistent production schedules. Additionally, standardized assets facilitate enhanced spare parts management by optimizing inventory levels. Companies can reduce the variety of parts needed, which lowers inventory holding costs and simplifies procurement processes. Faster replacement of components further minimizes equipment downtime, contributing to overall operational efficiency.
Moreover, standardization reduces training costs by consolidating training programs around fewer systems, ensuring that employees become proficient in operating standardized equipment. This not only cuts costs but also enhances overall productivity. Standardized systems streamline compliance with regulatory requirements by reducing the variations that need to be monitored and documented, thus alleviating the administrative burden associated with compliance audits. Furthermore, standardization allows for more efficient calibration processes, leading to reduced calibration costs and less frequent recalibration efforts. With a standardized asset base, pharmaceutical companies can also respond more quickly to changes in demand or production requirements, resulting in better resource allocation and reduced costs related to overproduction or stockouts.
Read more: Strategic Procurement in the Pharma Industry
Preparing for the Future
The pharmaceutical industry is evolving rapidly, with new technologies and market dynamics reshaping supply chain management. Businesses that embrace innovation and proactive strategies will be well-positioned to thrive in the future.
Key Trends to Watch:
- Digital Transformation: Increasing reliance on AI and blockchain for efficiency.
- Personalized Medicine: Supply chains adapting to meet the demand for customized treatments.
- Regulatory Changes: Staying compliant while managing costs.
Take Control of Your Pharmaceutical Supply Chain
Reducing costs in the pharma supply chain is a strategic necessity in today’s competitive landscape. By adopting advanced tools and partnering with experts like SpendEdge, your business can unlock new levels of efficiency and profitability.
Ready to revolutionize your supply chain? Contact SpendEdge today for tailored solutions to reduce costs and drive success. Fill out the contact form, and let’s start the conversation!