The packaging industry is undergoing a significant transformation, driven by the increasing adoption of automation and robotics. This shift is expected to push the global market for robotics in packaging to an impressive US$8.49 billion by 2027, reflecting a CAGR of 10.33% between 2022 and 2027. This surge in automation is driven by the packaging industry’s desire to streamline operations, improve efficiency, and enhance product quality.
One of the most common applications of robotics in packaging is pick and place tasks. Articulated robots with human-like robotic arms are widely used for picking products off conveyor belts and placing them into packaging. SCARA robots are particularly well-suited for these tasks, as they can operate with speed and precision. Robotic packaging systems also excel at palletizing, which involves arranging packaged products onto pallets for shipping. Cartesian robots, designed to operate on three axes, are often used for heavy lifting and palletizing tasks. These systems can quickly and safely palletize large quantities of goods, making them ready for the next stage in the distribution chain.
The benefits of robotic packaging extend beyond the production line. Automated warehousing systems, such as Automated Guided Vehicles (AGVs) and Autonomous Mobile Robots (AMRs), are being increasingly adopted to streamline the warehousing process. These systems can efficiently transport packaged goods, reducing the need for manual labor and improving overall productivity.
Driving factors of robotics in packaging
The adoption of robotics in the packaging industry is driven by several key factors, each contributing to the sector’s rapid transformation and growth. These include increased demand and e-commerce, labor shortages and safety concerns, improved accuracy and consistency, and the need for customization and sustainability.
Increased demand from E-commerce
- The surge in consumer demand, coupled with the exponential growth of e-commerce, has necessitated highly automated packaging processes.
- Automated packaging systems can process large volumes of orders quickly, ensuring timely deliveries and customer satisfaction.
- As businesses grow, robotic systems can be scaled up to handle increased workloads without a proportional increase in labor costs.
Improved accuracy and consistency
- Robotic packaging systems offer unparalleled accuracy and consistency, which are critical for maintaining product quality.
- With high precision, they can reduce the likelihood of errors in packaging which is critical to sensitive industries, such as pharmaceuticals and electronics. Robots can precisely measure and cut packaging materials, minimizing waste and optimizing resource use.
- Unlike human workers, robots do not suffer from fatigue, ensuring that every package is handled with the same level of care.
Customization and sustainability
- Modern robotic systems are versatile and can handle a wide range of product shapes and sizes, making them ideal for customized packaging solutions.
- This flexibility allows businesses to cater to individual customer preferences and market trends. Robots can optimize the use of packaging materials, reducing waste and supporting sustainability goals.
Labor shortages and safety concerns
- The difficulty in finding skilled labor for repetitive and physically demanding tasks is a persistent problem. Robots can perform these tasks efficiently, reducing dependency on human workers.
- Repetitive tasks in packaging can lead to worker injuries and fatigue. Robotic systems can operate at high speeds for extended periods without the risk of human error or physical strain, thus improving overall workplace safety.
Leading Innovations and disruptive technologies
The packaging industry is benefiting from several key innovations and disruptive technologies in robotics, which are revolutionizing how products are packaged, handled, and transported. These advancements include vision-guided robotics, collaborative robots (cobots), autonomous mobile robots (AMRs), and advanced grippers.
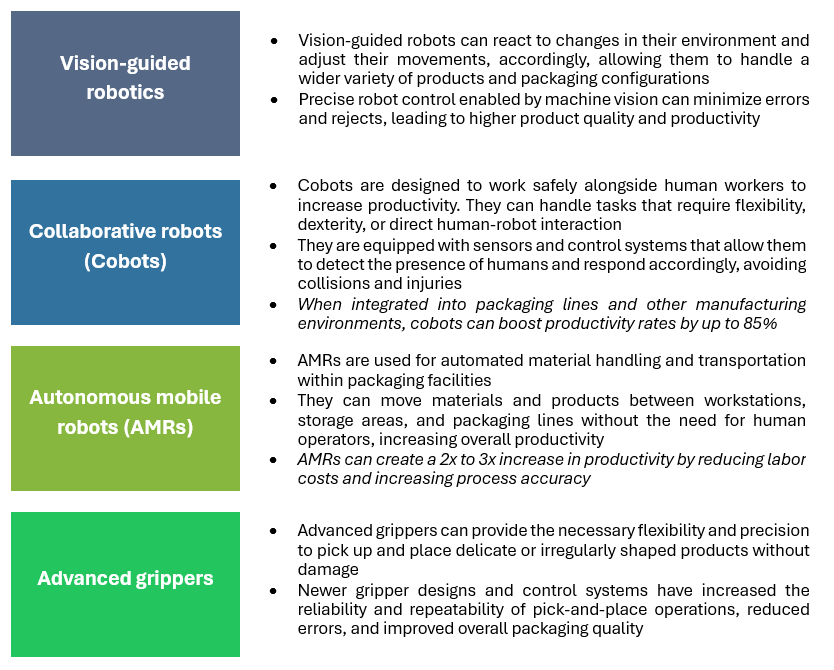
Leading innovators in robotics for the packaging industry
Several companies are at the forefront of developing and implementing robotic solutions for the packaging industry. These industry leaders provide advanced technologies that enhance efficiency, accuracy, and flexibility in packaging operations. Here are some of the key innovators:
ABB
ABB is a global leader in industrial automation and offers a wide range of robots for packaging applications. It is renowned for its comprehensive range of robotic solutions tailored to the packaging industry.
- The company recently opened a new packaging and logistics headquarters in the US to design and develop the next generation of AI-enabled robots for the packaging industry
- ABB’s packaging robots are used in diverse applications such as bakery, personal care, pharmaceuticals, and food handling. For example, the FlexPicker was used to automate the packaging of pancakes at HoneyTop Foods, achieving speeds of 400 pancakes per minute.
Fanuc
Fanuc is another major player in the robotics industry, providing a wide array of robots for packaging applications. It provides robots for palletizing, case packing, and material handling applications.
- Fanuc’s robots are designed for multiple tasks such as palletizing, case packing, and material handling. They are known for their versatility and ability to handle a variety of products and packaging formats. The robots are built for high-speed operations and heavy-duty applications, ensuring efficient and reliable performance in demanding packaging environments
- It offers integrated robotic systems that combine hardware and software to streamline packaging processes. Their solutions include vision systems, force sensors, and advanced control software
- With a strong global presence, it provides extensive support and service networks, ensuring that clients have access to the resources they need to maintain and optimize their robotic systems.
Kuka Robotics
Kuka Robotics is a prominent name in robotics, known for its innovative solutions in the packaging industry.
- It offers a wide range of robots designed for various packaging tasks, including handling, packing, palletizing, and quality inspection. Their robots are known for their precision, flexibility, and robustness. It integrates advanced technologies such as AI, machine learning, and IoT to create intelligent robotic systems. These systems can adapt to changing packaging requirements and improve overall operational efficiency.
- Its cobots are designed to work safely alongside human workers, enhancing productivity and safety in packaging operations
- It provides customized robotic solutions tailored to the specific needs of their clients. Its systems are designed to be easily reconfigured and scaled to accommodate different packaging requirements.
Universal Robots
Universal Robots is a leading manufacturer of cobots that are widely used in the packaging industry. Its cobots are designed to be easy to program and deploy, making them accessible to businesses of all sizes. Its intuitive interface allows operators to set up and reprogram the robots quickly. It offers integrated vision and gripping solutions for UR cobots to automate packaging workflows.
Bosch Packaging Technology
Bosch Packaging Technology integrates robotics with complete packaging lines, offering customized solutions that enhance efficiency and flexibility. It provides fully integrated packaging systems that combine robotic automation with traditional packaging machinery. This integration ensures seamless operations and optimal performance. Key aspects of Bosch’s offerings include:
- Turnkey packaging lines with robotic automation for industries like food, pharmaceuticals, and cosmetics
- Customized solutions to meet specific customer requirements for flexibility, speed, and product handling
- Provides services like line optimization, maintenance, and training to support packaging operations
Top user companies and success stories
Coca-Cola
Coca-Cola has automated palletizing systems in some of its facilities and distribution centers around the world. By embracing robotic automation for palletizing and depalletizing, Coca-Cola enhanced safety, boosted productivity, and streamlined its packaging operations.
- Coca-Cola Amatil in New Zealand installed a fully automated robot-based order-picking system called ACPaQ from Swisslog, which combines robotics solutions for palletizing and depalletizing with shuttle technology. This allows customized and scalable pallets to be created at high throughput rates of up to 1,000 cases per hour.
- Coca-Cola Canada Bottling is investing over US$70 million to build a cutting-edge robotic warehouse facility in Calgary, equipped with an automated storage and retrieval system. This will consolidate local storage and showcase the company’s foray into automation.
Procter & Gamble (P&G)
P&G implemented robotic palletization systems in its operations, significantly improving productivity and worker safety.
- P&G showcased its robotic palletization technology at the 2020 Consumer Electronics Show (CES), demonstrating how the company is leveraging automation and data-driven innovations to enhance its packaging and supply chain operations
- The robotic palletizers allow P&G to handle a wide variety of product sizes and shapes, providing the flexibility to adapt to changing packaging needs
- By implementing these advanced robotic palletization systems, P&G has been able to boost the efficiency and productivity of its packaging lines while also enhancing worker safety and reducing the risk of injuries
Nestlé
Nestlé employs robots for high-speed picking and placing of products, ensuring consistent quality and efficiency. These robots can handle a wide range of products with precision and speed.
- By automating picking and placing tasks, Nestlé ensures that each product is handled with the same level of care, maintaining high-quality standards and reducing errors
- Nestlé continuously explores innovative applications of robotics to enhance their packaging capabilities, including integrating robots with vision systems and AI for more advanced and adaptable packaging solutions.
Benefits of robotics in packaging
The integration of robotics in packaging operations delivers significant benefits in terms of cost savings, productivity gains, quality improvements, worker safety, and supply chain resilience. Following is some of the benefits and key advantages of robotics in packaging:
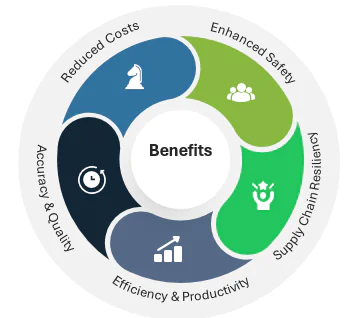
- Operates 24/7 without breaks, leading to increased production output and maximizes machinery utilization
- Minimizes material waste and product damage, reducing operational costs
- Operates 24/7 without breaks, leading to increased production output and maximizes machinery utilization
- Takes over repetitive and potentially dangerous tasks in hazardous environments or with dangerous materials
- Reduces the risk of worker injuries and improving overall workplace safety
- Performs tasks with high precision and consistency, minimizing errors and ensuring quality control.
- Advanced vision systems and sensors allow robots to accurately identify, pick, and place products even with variations in size, shape, and orientation
- Helps reduce waste generated from faulty packaging by minimizing errors and defects, leading to more efficient use of materials and resources
- Companies can adapt to fluctuating demand and production volume, maintaining production and distribution during disruptions
- Automated systems improve the reliability and consistency of packaging operations, enhancing supply chain resilience
- Operates at higher speeds and with greater consistency than manual processes, leading to increased throughput
- Handles multiple products and packaging configurations simultaneously, streamlining the entire packaging line
- Maintains consistent performance, ensuring that each task is performed to the same standard every time.
Challenges in implementing robotics in packaging
While robotics offers numerous advantages for the packaging industry, there are several challenges that companies must address to successfully implement these technologies. High initial investment costs, integration complexity, the need for specialized technical expertise, and limitations in product and line flexibility are some of the major challenges that companies must address to successfully implement these technologies.
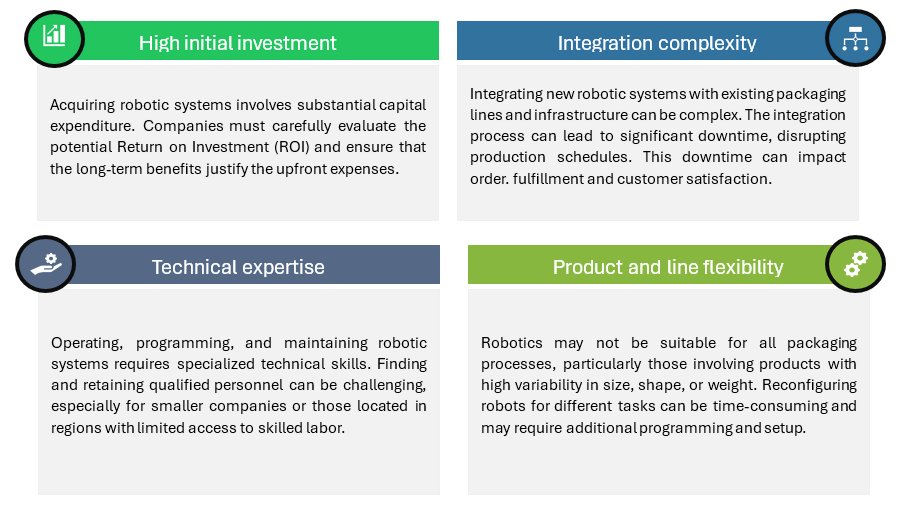
How Robotic Systems can help in overcoming challenges?
Integrating robotic systems with existing packaging lines and infrastructure can be a complex and time-consuming process, presenting significant challenges for many companies. This complexity stems from various factors, including compatibility issues, infrastructure adaptation, system integration, downtime and disruption, lack of technical expertise, and cost considerations. Despite these hurdles, the advantages of integrating robotic systems such as increased efficiency, precision, and scalability, make it a worthwhile investment. By leveraging the expertise and customized solutions offered by robotics partners, companies were able to successfully overcome the challenges and integrate robotic automation into their packaging workflows. The following are some of the case studies highlighting the challenges faced by the companies and solutions offered by the robotics company to overcome those challenges:
- American Eagle Packaging, a US-based packaging and containers manufacturing company, was able to overcome the challenge of integrating robots into their existing packaging lines by partnering with a robotics company that provided a customized solution. The partnership allowed American Eagle Packaging to implement a robotic system that seamlessly integrated with their existing equipment, minimizing disruption to their operations.
- By leveraging the expertise and customized solutions offered by robotics partners, American Eagle Packaging was able to successfully incorporate robotic automation into their packaging workflows. This highlights a successful strategy for overcoming the integration challenges often associated with implementing new robotic technologies.
The future of robotics in packaging
Following are some of the future robotics trends, technologies, and innovations to impact packaging industry:
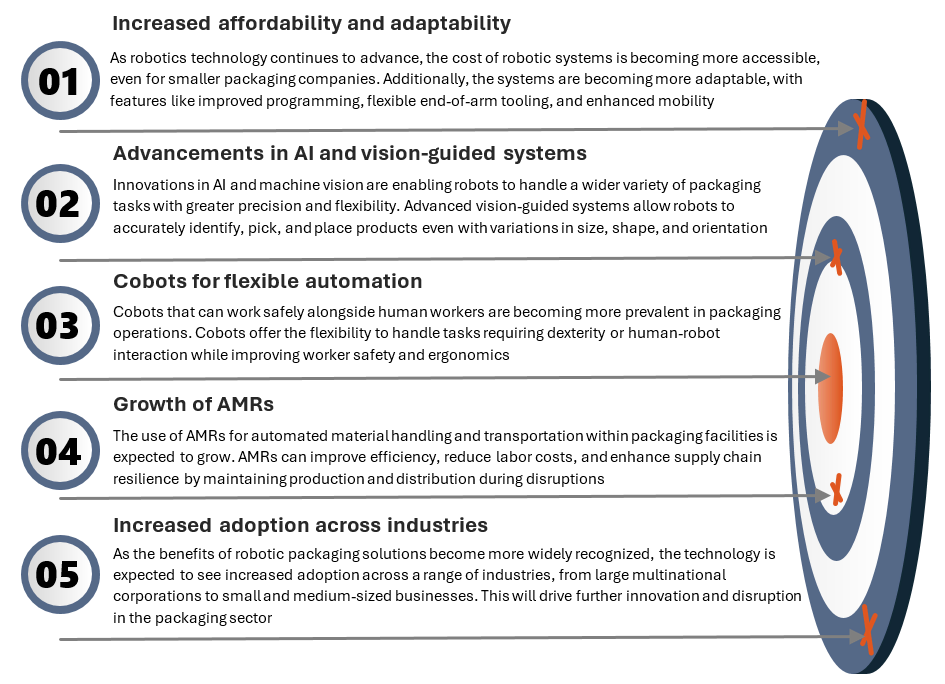
The future of robotics in packaging is set to transform the packaging industry. As technology advances, robotics in packaging is poised to bring even greater innovations and improvements. The integration of advanced robotics, AI, and automation technologies will be crucial in driving efficiency, quality, and sustainability in the packaging industry. Manufacturers that embrace these innovations will be well-positioned to meet the growing demands of the future packaging landscape.