Key takeaways
- Technological Advancements: The Metal Fabrication Equipment Market is growing due to advancements in automation and precision metal machining, essential for mass manufacturing.
- Industry Dependence: Key sectors like automotive, aerospace & defense, and the semiconductor industry drive demand, ensuring sustained market growth.
- Operational Challenges: High raw material costs and import/export prohibitions pose challenges, but technological improvements help mitigate these issues.
- Future Outlook: Integration of Industry 4.0 innovations and efficient material handling are expected to propel the global metal fabrication equipment market forward.
The modern wonders of the world are all possible due to advances in construction technology and material science. Although technological advancement is growing at an unprecedented rate, it’s the small and simple things that still matter. Sheet metal fabrication is still as important in construction and manufacturing as it was decades ago. Sheet metal fabrication equipment is used to cut and provide shapes to sheet metal components and also involves the process of material removal or material deformation. It comes as no surprise that the sheet metal fabrication equipment market is ever-growing. The growth of end-user industries such as construction, heavy equipment, and energy can be attributed to the growth of the sheet metal fabrication equipment market. In addition, the automotive industry is another major end-user industry, which is fueling market growth. However, it’s not all easy for the procurement teams in this market to conduct business.
Metal Fabrication Equipment Market Size
The Metal Fabrication Equipment Market is witnessing significant growth due to advancements in manufacturing processes and increasing demand from various industrialized countries. Metal fabrication involves the creation of metal structures through cutting, bending, and assembling processes. The market encompasses a wide range of equipment such as machine tools, tooling and fabricating equipment, and tool presetting machines used by manufacturers in different sectors including automotive industry and aerospace & defense. One of the key drivers of this market is the demand from the automotive industry, which requires precise and durable components. Manufacturing companies are investing in advanced machinery to enhance their production capabilities and efficiency. Additionally, technical improvements in machining environments and the introduction of innovative machine tools are propelling the market forward.
However, the metal fabrication market faces challenges such as the high price of raw materials and import/export prohibitions which can impact the cost-effectiveness of operations. The availability and cost of raw materials play a crucial role in determining the overall profitability for manufacturers. Despite these challenges, the market is expected to grow due to the ongoing need for fabricated metal products across various industries.
In the metal fabrication equipment market, scrap management and reducing waste are critical concerns. Efficient use of materials and recycling of scrap can significantly reduce costs and environmental impact. Moreover, the demand for machine tools market is increasing as companies seek to improve precision and reduce downtime in their production processes. As the market evolves, engineers and manufacturers are focusing on developing more sophisticated tooling and fabricating equipment to meet the growing demand for high-quality metal products. The continuous advancement in technology and the need for efficient machining environments are expected to drive the metal fabrication equipment market further in the coming years.
Procurement Challenges in the Sheet Metal Fabrication Equipment Market
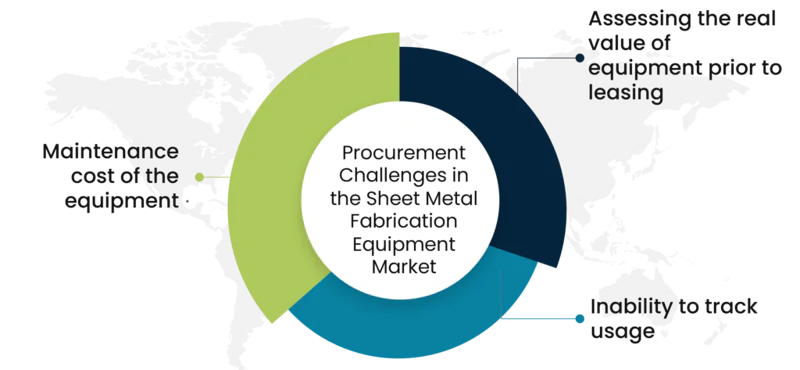
Maintenance cost of the equipment
The overall maintenance cost for sheet metal fabrication equipment consists of the time and money that was spent on the corrective actions and the loss of production time that results in direct revenue loss for the organization. Additionally, the age of the equipment, condition of the equipment, and amount of utilization of the sheet metal fabrication equipment also impacts the overall spend on maintenance. As a result of increasing cost of maintenance, the TCO of sheet metal fabrication equipment is increasing, taking it beyond the purchasing power of small and medium scale buyers.
Inability to track usage
Buyers across different industries are not tracking parameters such as idle machine time and proper estimation of the use of equipment. This results in the sub-optimal utilization of sheet metal fabrication equipment across different industries. As a result, third-party professionals need to be hired to conduct surveys to assess the true utilization rate of the equipment accurately.
Assessing the real value of equipment prior to leasing
Buyers across different end-user industries prefer procuring sheet metal fabrication equipment on lease. It helps to reduce the CAPEX and optimize the profit margins for buyers. However, buyers find it difficult to assess the value of sheet metal fabrication equipment prior to leasing as it requires checking parameters such as the history of usage and utilization rates. As a result, buyers find it difficult to assess the residual value of the equipment prior to its procurement. To ascertain the true value, buyers must take assistance from industry experts to understand the residual value of the equipment before leasing the equipment.
To avoid and tackle such procurement challenges, buyers in the sheet metal fabrication equipment market should invest in preventive maintenance and try to outsource the maintenance of equipment. Also, it can help if buyers hedge against raw material price fluctuations as it eases the financial burden.
Solutions for effective procurement
Cost Analysis and Negotiation:
Analyze the total cost of ownership (TCO) rather than just the purchase price, considering factors like maintenance, energy consumption, and training costs. Negotiate prices and terms with suppliers to secure favorable agreements while maintaining quality standards.
Market Research and Supplier Evaluation:
Conduct thorough market research to understand the latest trends, technology advancements, and supplier capabilities in the sheet metal fabrication equipment market. Create a list of potential suppliers and assess them based on factors such as quality, reliability, pricing, delivery times, and after-sales support.
Legal and Compliance:
Stay informed about industry regulations and compliance requirements related to sheet metal fabrication equipment. Ensure all contracts and agreements adhere to legal standards and are regularly reviewed.
Metal Fabrication Equipment Market Trends Source
The emergence of Industry 4.0, also known as the Internet of Things (IoT), represents a significant trend that is anticipated to deeply impact tooling and fabricating equipment, particularly in relation to the transmission of information to machine tools and engineers/operators. Smart tooling is projected to offer real-time feedback on issues such as vibration, and to promptly notify the engineer. The transition to Industry 4.0 commences with machining environments that demonstrate high consistency in day-to-day operations. Tool presetting plays a pivotal role in initiating this process. Once the tool holder assembly is preset, data can be directly transmitted to the machine tool (resulting in time savings and averting potential machining errors) or it can be transferred to an RFID chip integrated into the tool holder.
Manufacturers consider the presetting process as a significant factor in reducing scrap during production. The demand for Industry 4.0 solutions is on the rise as companies gravitate towards consistently high levels of productivity in machining operations. The market’s growth potential is being propelled by increasing trends of digitization and internet penetration, driven by various sectors’ heightened emphasis on efficiency and profitable productivity. Recent advancements in digital technologies and industrial computerization have begun to cultivate the potential to disrupt the industrial value chain. The advent of the fourth industrial revolution (4.1) has enabled businesses to benefit from enhanced productivity, customized products, reduced costs, and, most importantly, the development of new revenue and business models.
Amid the global market’s upheaval due to the COVID-19 pandemic, digitalization across industries is rapidly accelerating. This presents a new opportunity for digital leaders to devise and adopt innovative solutions to expedite digital transformation at all organizational levels. The outbreak of the coronavirus is expediting the onset of the fourth industrial revolution (Industry 4.0), compelling businesses across various sectors to embrace heightened levels of Internet of Things (IoT) technology and workflow. The global supply chain is experiencing unparalleled instability as a result of the COVID-19 pandemic, which has impacted the entire globe. Some manufacturing firms have ceased production entirely, while others have witnessed a significant decline in demand, and a few have experienced an upsurge in demand.
Read more about the procurement challenges in the sheet metal fabrication equipment market along with procurement best practices, pricing models, supply market insights, and market challenges in SpendEdge’s upcoming report on the global sheet metal fabrication equipment market.
Conclusion
The Metal Fabrication Equipment Market is set to continue its growth trajectory, driven by advancements in automation, precision metal machining, and the increasing demands of mass manufacturing. Despite challenges like the high price of raw materials and import/export prohibitions, the market is thriving due to the vital role sheet metal fabricators play in the manufacturing space. Key application industries such as the automotive industry, aerospace & defense, and the semiconductor sector rely heavily on advanced metal fabrication equipment for efficient material handling, reduced operating costs, and shortened cycle times. The ongoing technological improvements and the integration of Industry 4.0 innovations are expected to bolster market growth further. As detailed in the market report, the global metal fabrication equipment market is poised for robust expansion, with significant opportunities for metal producers and manufacturing companies to optimize their production processes and maintain a competitive edge.