Key takeaways
- Advanced Cost Analysis Tools: Utilizing modern manufacturing cost analysis software is essential for managing overhead and component costs effectively.
- Data-Driven Decisions: Leveraging should cost analysis and component spend analysis provides critical cost insights, enabling precise data-driven cost decisions.
- Optimization and Savings: These tools help identify significant savings opportunities and ensure effective procurement estimates and renegotiation goals.
- Competitive Advantage: Integrating advanced cost analysis frameworks supports efficient machining and enhances cost-reduction plans, ensuring substantial potential savings.
Cost modeling involves the analysis of production costs, labor costs, material costs, and profit margins to determine the true cost of a product or service. It helps organizations understand the supplier’s pricing strategy and also be able to determine the actual price they should pay for a particular component or part. Cost modeling is a common activity in large organizations and has found wide acceptance all over the globe. Organizations are now driving business decisions based on insights derived from a large amount of data available through several credible sources. However, the small and medium manufacturing enterprises are still to catch on to this new trend in the market. This is largely due to the lack of technological infrastructure as well as the expertise to perform complex and challenging tasks like cost modeling by these organizations.
An organization cannot create a competitive advantage based on product innovation alone. To gain an edge and maintain a leadership position in the market, businesses have to focus on a robust supply chain management strategy. For this, the organization has to leverage cost modeling tools to identify the costs involved in procuring raw materials from various suppliers to receive top-quality materials at the best possible price. Cost modeling helps the organization to facilitate cost savings and drive profitability throughout the supply chain.
What Is Manufacturing Cost Estimation?
Manufacturing cost estimation is the collection of methodologies and tools used to estimate the final cost of a finished product. This analysis informs major manufacturing decisions, such as which products will be profitable and whether suppliers offer a reasonable price or current product offerings need to be adapted so that they remain cost-competitive.
Why Should Small and Medium Manufacturing Businesses Use Cost Modelling Software?
For small and medium manufacturing businesses (SMBs), cost modeling helps improve their trend forecasting ability if coupled with predictive analytics. You ask how? Here’s how.
- Manufacturing and product development entail converting raw materials into a finished product. This means the organizations have to source and procure raw materials, process them to add value to them and distribute the final product.
- The costs for each activity involved in the source-to-customer process are not constant, instead, they vary from time to time. These SMBs need to forecast different SKUs, costs sales volumes, and revenues, and derive insights from the information available which is a difficult task as it requires additional knowledge and cost modeling skills.
- SMBs produce commodities known as intermediate goods that are used to produce finished products. The cost of these intermediate goods determines the cost of the final product. The typical customers for these intermediate goods are large organizations or original equipment manufacturers (OEMs) for instance an automotive company or a transportation company.
- For an SMB to survive in the market and make profits, it should be aware of its actual input costs and the effect it has on the finished product. Therefore, cost modeling enables SMBs to identify these costs, determine their impact on the final cost, and help SMBs establish accurate input costs. Hence, monitoring the process of such commodities, and identifying the factors that impact the total cost and eventually, the profit margins is vital for the company.
- A small and medium manufacturing business should integrate a cost-based approach and base its pricing strategy on the insights derived from an effective cost modeling tool.
At SpendEdge, we help organizations with real-time and accurate price tracking of input materials and commodities and provide supplier cost analysis to gain a detailed understanding of each component to enable procurement professionals to source the right products at the best price and thereby drive cost savings.
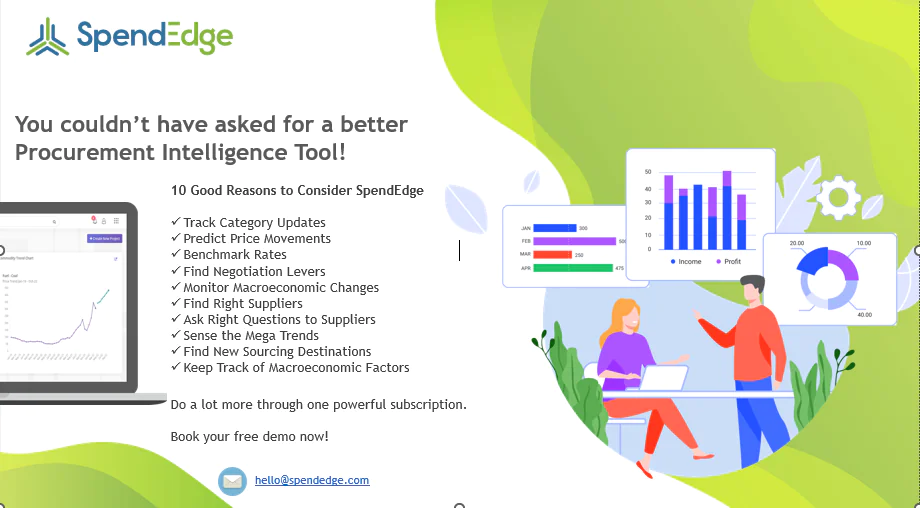
What are the different cost modeling tools
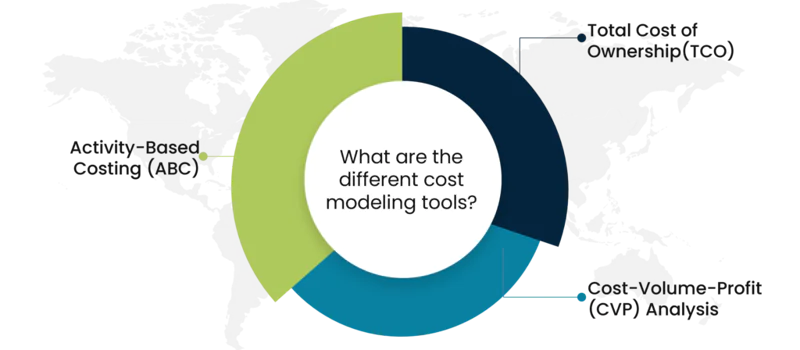
Activity-Based Costing (ABC):
Activity-Based Costing is a cost modeling tool that assigns costs to specific activities or processes within an organization. It involves identifying and analyzing the activities that consume resources and then allocating costs based on the drivers or factors that cause those activities. ABC provides a more accurate and detailed understanding of costs by considering the various activities involved in producing goods or delivering services. This tool helps organizations make informed decisions regarding pricing, product profitability, and process improvement.
Total Cost of Ownership(TCO):
Total Cost of Ownership is a cost modeling tool that evaluates the overall costs associated with owning and operating a particular asset or system over its entire lifecycle. TCO takes into account not only the initial purchase price but also factors such as maintenance, repairs, operating costs, and disposal costs. By considering the complete cost picture, TCO enables organizations to make more informed decisions when comparing different options or investments. It helps identify the most cost-effective solutions and can be particularly useful in procurement decisions or when evaluating long-term investments.
Cost-Volume-Profit (CVP) Analysis:
Cost-volume-profit analysis is a cost modeling tool that examines the relationship between costs, volume or quantity produced, and sales revenue. It helps organizations understand the impact of changes in volume or sales on their profitability. CVP analysis considers fixed costs, variable costs, selling price per unit, and the sales mix to determine the breakeven point, target profit levels, and the level of sales required to achieve those targets. This tool assists in decision-making related to pricing strategies, product mix, and sales volume planning.
The evolution: Manufacturing Cost Estimation techniques
Any manufacturing process needs to use at least some basic cost estimation to ensure profitability. At the lowest level, this task might simply involve using recent market prices to tally up expected input costs, then adding a mark-up for packaging, shipping, and profit. If this estimate appears to be above current market prices, production isn’t viable.
Companies that take this particular approach have often relied on homegrown databases of historical information. In 1985, MS Excel was introduced and has become the most common tool used to support this costing strategy. This approach may work fine if you are a small supplier with just a few cost estimators all working in the same office. However, once you are faced with designing, manufacturing, and sourcing on a national or global scale, it simply becomes too complicated to try and manage the extreme number of cost variables in a spreadsheet.
Direct costs like wages and raw materials are not only tied to the efficiencies of underlying production processes but are themselves potential variables when estimating design alternatives.
Also, first released in the early-mid 1980s was the first commercially available, specialized manufacturing cost estimation software. Most of these software applications were designed to meet the needs of cost estimators and required significant training and expertise to utilize effectively. Furthermore, these early systems did not leverage modern database technology and often caused significant cost model consistency challenges for design and sourcing teams located in different geographic regions.
By the early 2000s, manufacturers were starting to look for manufacturing cost analysis systems that would allow designers and engineers to quickly and easily understand if their new design—represented by a 3D-solid CAD model—is over or under target cost early in the design process. Sourcing managers were also beginning to see the need for a “should cost” estimation with rich manufacturing detail to enable more fact-based cost-reduction negotiations with their suppliers. And, cost estimation teams—often severely understaffed—wanted more of an automated costing system that allowed for things like batch costing of hundreds of CAD models to identify cost outliers. Evolving job requirements like these are progressively moving manufacturers toward solutions that have a modern database architecture, are available through a role-based web browser, and have extensive libraries of material and machine data.
Modern manufacturing cost analysis software provides critical component costs, enabling effective cost analysis and aiding in renegotiation strategies in response to price increases. These tools offer valuable insights for manufacturing decisions, incorporating forecast data to help identify and manage cost drivers. By facilitating cost-reduction negotiations and allowing manufacturers to renegotiate with suppliers, these systems support efficient manufacturing processes.
Incorporating product cost management strategies helps manufacturing companies control manufacturing facility expenses and better manage product cost outliers. Overall, leveraging advanced software solutions for manufacturing cost analysis ensures a more accurate and efficient approach to managing costs in a highly competitive market.
To know more about cost modeling cost models in procurement, cost modeling tools, and cost modeling software:
Conclusion
In today’s competitive market world, integrating advanced manufacturing cost analysis software into manufacturing process groups is crucial for controlling overhead costs and optimizing component costs. By utilizing tools for should cost analysis and component spend analysis, cost engineering teams can gain deep cost insights and identify significant savings opportunities. These systems enable data-driven cost decisions and help manufacturers stay ahead of current prices, ensuring effective procurement estimates and renegotiation goals. Leveraging product cost data and spend per part information allows for precise cost-reduction plans and empowers cost specialists to secure better supplier prices. Ultimately, a robust cost analysis framework supports efficient machining, enhances cost-reduction plans, and achieves substantial potential savings.